著者について:
著者:Hefei Smarter Technology Group Corp.
1958年に設立され、 合肥スマートターテクノロジーグループ株式会社 は、30 年以上にわたり中国でケーブル機械の大手メーカーとして活躍しています。1985 年以来、特殊なケーブル機械に注力してきた同社は、精密エンジニアリングと細心の職人技で高い評価を得ています。今日、Hefei Smarter はケーブル機械の大手メーカーであるだけでなく、RTP (強化熱可塑性パイプ) やオフショア パイプ機械の有名なメーカーでもあります。
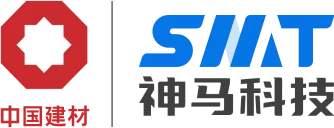
アルミニウム合金ロッドの製造においては、品質と信頼性を確保するために業界標準を遵守することが重要です。これらの標準はロッドの性能を保証するだけでなく、生産プロセスの安全性と効率性も促進します。
合金組成規格
アルミニウム合金ロッドは、ASTM (米国材料試験協会) や ISO (国際標準化機構) などの規格で定義された特定の合金組成から作られています。これらの規格では、アルミニウムと銅、亜鉛、マグネシウム、シリコンなどの合金元素の正確な比率が規定されています。各合金組成は、耐腐食性、導電性、強度などの望ましい機械的特性を実現するように調整されています。このカスタマイズにより、ロッドは電気配線から航空宇宙の構造部品まで、さまざまな用途に適しています。
寸法仕様
アルミニウム合金ロッドの製造では、精度が重要です。ASTM または国家規格団体によって設定された規格では、ロッドの直径、長さ、真直度、表面仕上げの寸法公差が詳細に規定されています。これらの仕様を順守することで、下流のアプリケーションとの一貫性と互換性が保証されます。たとえば、自動車製造で使用されるロッドは、エンジンやシャーシ コンポーネントに適切にフィットして性能を発揮できるように、厳しい寸法公差が求められます。
機械的性質
規格では、アルミニウム合金ロッドが示さなければならない引張強度、降伏強度、伸び、硬度などの機械的特性が指定されています。メーカーは、これらの特性が規格で概説されている要件を満たしているか、それを超えていることを確認するために、厳格なテストを実施しています。さまざまな動作条件下でのロッドの耐久性と信頼性を検証するために、微細構造分析や疲労テストなどの高度な技術が採用されています。
テストと品質管理
品質管理プロセスは、業界標準に準拠するために不可欠です。製造業者は超音波検査などの非破壊検査方法を使用して内部欠陥を検出し、ロッドの完全性を確保します。規制機関からの認証により、ロッドが品質と安全性の基準を満たしていることが証明されます。継続的な改善活動により、生産プロセスが効率的に維持され、進化する標準と顧客の期待に沿ったものになります。
環境および安全基準
アルミニウム合金棒の製造では、持続可能な慣行がますます重要になっています。基準は、リサイクル慣行を促進し、製造プロセス中の二酸化炭素排出量を削減することで、環境問題に対処します。たとえば、エネルギー効率の高い技術と廃棄物削減戦略を実施して、環境への影響を最小限に抑えます。安全基準は、生産施設が労働者を保護し、溶融金属や危険物の取り扱いに伴うリスクを最小限に抑えるプロトコルに準拠していることを保証します。
結論
アルミニウム合金棒の製造業者は、業界標準を厳格に遵守することで、品質、性能、安全性に対する取り組みを維持しています。これらの標準は、製造プロセスをガイドするだけでなく、エンドユーザーが信頼性と持続可能性に関する厳しい基準を満たす製品を受け取ることを保証します。製造に携わっている場合でも、アルミニウム合金棒の適用を検討している場合でも、これらの標準を理解することは、情報に基づいた決定を下し、最適な結果を得るために不可欠です。