In the modern world, cables and wires are the unsung heroes that power our daily lives. From electricity transmission to telecommunications, these essential components form the backbone of our interconnected society. Behind the scenes, a complex web of machinery ensures the efficient production of cables and wires to meet the ever-growing demands of industry and consumers alike. Let's delve into the fascinating world of cable and wire manufacturing and explore the crucial role played by different machines in this process.
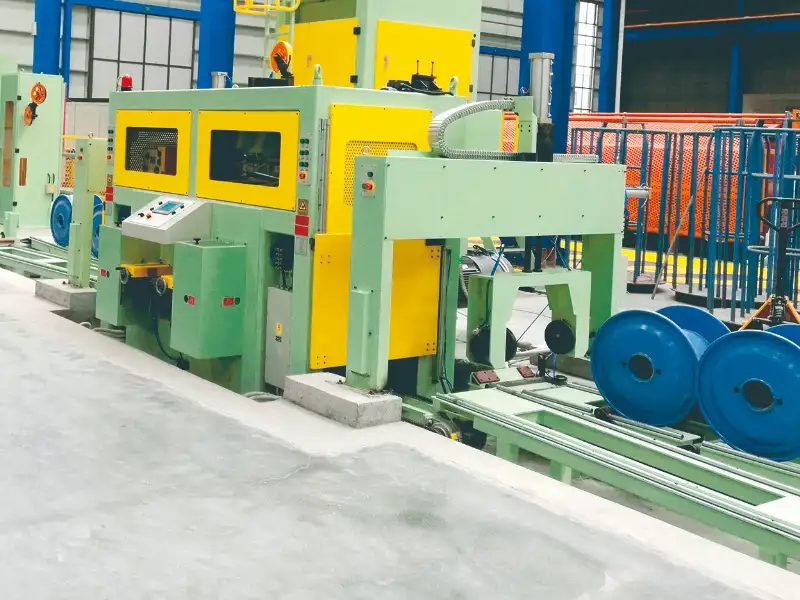
Wire Drawing Machine:
At the heart of cable and wire manufacturing lies the wire drawing machine. This essential piece of equipment transforms raw materials such as copper, aluminum, or steel into wires of various diameters. The process involves pulling the metal through a series of dies to reduce its diameter while increasing its length. Wire drawing machines come in various configurations to accommodate different materials and production requirements, ensuring precise control over wire dimensions and quality.
Wire drawing machines operate on a simple yet highly efficient principle. They consist of a drawing capstan, a drum or spool for storing the raw material, and a series of dies through which the material is pulled. The wire is fed through the dies, which progressively reduce its diameter until it reaches the desired size. Tension control systems ensure uniform drawing and prevent breakage, while lubrication systems minimize friction and extend die life.
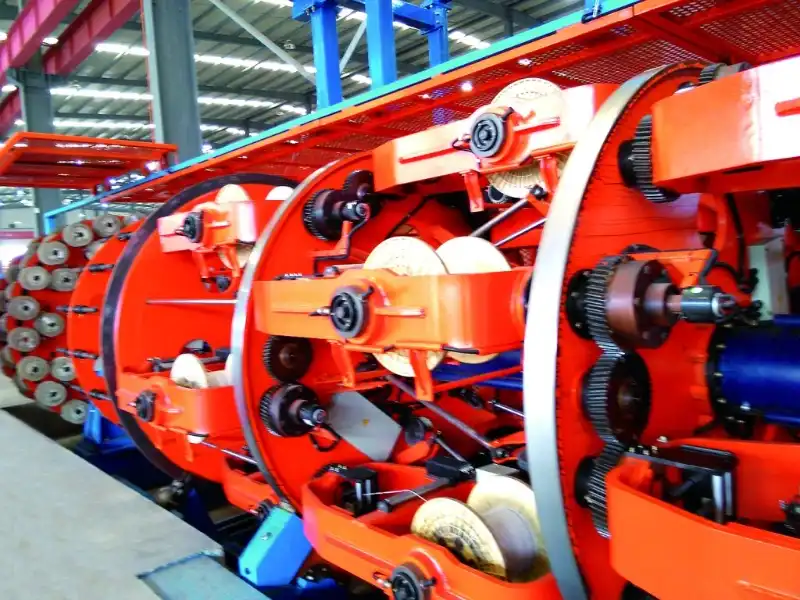
Stranding Machine:
Once the wires are drawn to the desired diameter, they undergo stranding to create cables capable of carrying higher currents or supporting heavier loads. Stranding machines twist multiple wires together in a helical pattern, forming a flexible and robust cable structure. These machines come in several types, including tubular, planetary, and rigid cage stranders, each suited to specific applications and wire configurations. Advanced stranding machines feature computerized controls to adjust twist rates, lay lengths, and tension levels, ensuring consistent cable performance.
Stranding machines are essential for producing cables with superior mechanical strength and electrical conductivity. They consist of multiple bobbins or spools of wire arranged around a central core. As the core rotates, the bobbins unwind, and the wires are twisted together according to the desired pattern. Tension control systems ensure uniform twist rates and prevent wire breakage, while traversing mechanisms distribute the wires evenly to achieve a uniform lay length.
Insulation and Jacketing Lines:
To protect the conductors from environmental factors and electrical interference, cables undergo insulation and jacketing processes. Insulation lines apply layers of insulating material, such as PVC, XLPE, or rubber, around the conductors, while jacketing lines add outer protective layers for additional durability. These lines consist of extruders, crosshead dies, cooling baths, and take-up units, all working together to coat the cables with uniform insulation and jacketing materials. Precise temperature control and die design are critical to achieving optimal insulation thickness and adhesion properties.
Insulation and jacketing lines are essential for enhancing the performance and longevity of cables in harsh operating conditions. They utilize extrusion technology to apply molten polymer compounds to the surface of the conductors, forming seamless protective coatings. Cooling systems rapidly solidify the polymer layers, while take-up units spool the finished cables onto reels for further processing. Advanced monitoring systems detect defects and deviations in real-time, ensuring consistent product quality and compliance with industry standards.
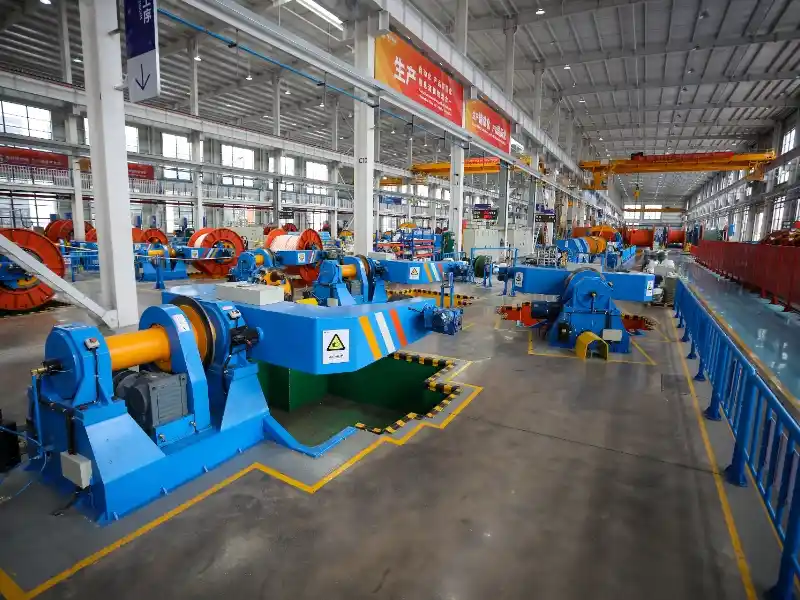
Cabling and Twisting Machines:
In applications requiring multiple conductors, such as power distribution or data transmission cables, cabling and twisting machines play a vital role in assembling individual wires into cable assemblies. These machines arrange the conductors in predetermined configurations, such as parallel, concentric, or helical layouts, before twisting them together to form the final cable structure. Advanced cabling machines feature servo-driven payoffs and traversing systems for precise conductor positioning, ensuring consistent cable geometry and electrical performance.
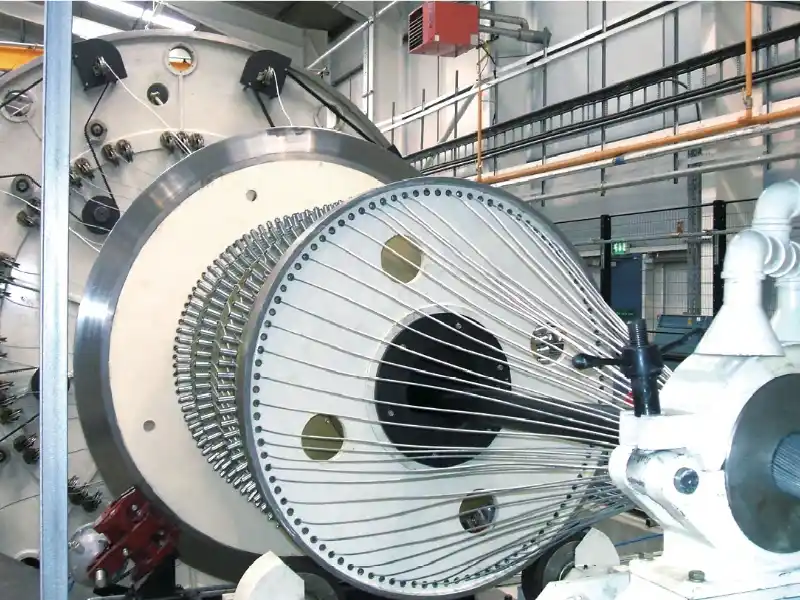
Sheathing and Armoring Equipment:
For cables deployed in harsh environments or industrial settings, additional layers of protection may be required. Sheathing and armoring equipment apply metallic or non-metallic shields and armor wires around the cable cores to enhance mechanical strength and resistance to abrasion, impact, and chemical exposure. Sheathing lines feature extruders with specialized dies and cooling systems to apply seamless protective coatings, while armoring machines twist and interlock steel wires or tapes around the cables with controlled tension and pitch angles.
In conclusion, the manufacturing of cables and wires is a sophisticated process that relies on a diverse array of machinery to transform raw materials into functional and reliable products. From wire drawing and stranding to insulation, cabling, and sheathing, each step is meticulously orchestrated to ensure quality, efficiency, and consistency. As technology continues to advance, innovative machines and automation solutions will drive further improvements in cable and wire manufacturing, enabling the seamless integration of power, communication, and data transmission networks in the digital age.
The world of cable and wire manufacturing is intricately supported by a diverse range of specialized machinery. As a leading manufacturer of wire and cable making machines, along with cutting-edge RTP (Reinforced Thermoplastic Pipe) and offshore pipe machinery, we recognize the crucial role these technologies play in driving innovation and efficiency across industries.
Our extensive portfolio of machinery encompasses wire drawing machines, stranding machines, insulation and jacketing lines, cabling and twisting machines, as well as sheathing and armoring equipment. Each of these machines is meticulously designed and engineered to meet the demanding requirements of modern cable and wire production.
Moreover, our commitment to quality extends beyond manufacturing excellence. As an exporter, we pride ourselves on offering exceptional export services, ensuring seamless transactions and timely deliveries to our global clientele. We understand the importance of reliable partnerships and strive to be a trusted collaborator for businesses seeking high-performance solutions.
Choosing Smarter as your partner means gaining access to cutting-edge technology and industry expertise. Our focus on continuous improvement and customer satisfaction positions us as a preferred supplier in the wire and cable manufacturing sector. Whether you are looking to expand your production capacity, improve product quality, or enhance operational efficiency, we are here to support your goals with innovative solutions and unparalleled service.
In a rapidly evolving marketplace, investing in advanced machinery and reliable partnerships is key to staying competitive. Smarter stands ready to empower your business with state-of-the-art equipment and a commitment to excellence, enabling you to navigate the complexities of cable and wire manufacturing with confidence and success.