About the Author:
Written by Hefei Smarter Technology Group Corp.
Founded in 1958, Hefei Smarter Technology Group Corp. has been a leading manufacturer of cable machinery in China for over three decades. With a focus on specialized cable machinery since 1985, the company has built a reputation for precision engineering and meticulous craftsmanship. Today, Hefei Smarter is not only a leading manufacturer of cable machinery but also a renowned manufacturer of RTP (Reinforced Thermoplastic Pipe) and offshore pipe machinery.
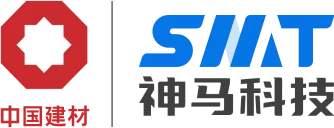
Drum twisters are essential machines in the wire and cable industry, used to twist wires and cables together for enhanced performance and durability. The two main types of drum twisters available in the market—single-twist and double-twist machines—serve different purposes and applications. Below is an exploration of these types and their specific uses in wire and cable manufacturing.
Table of Contents
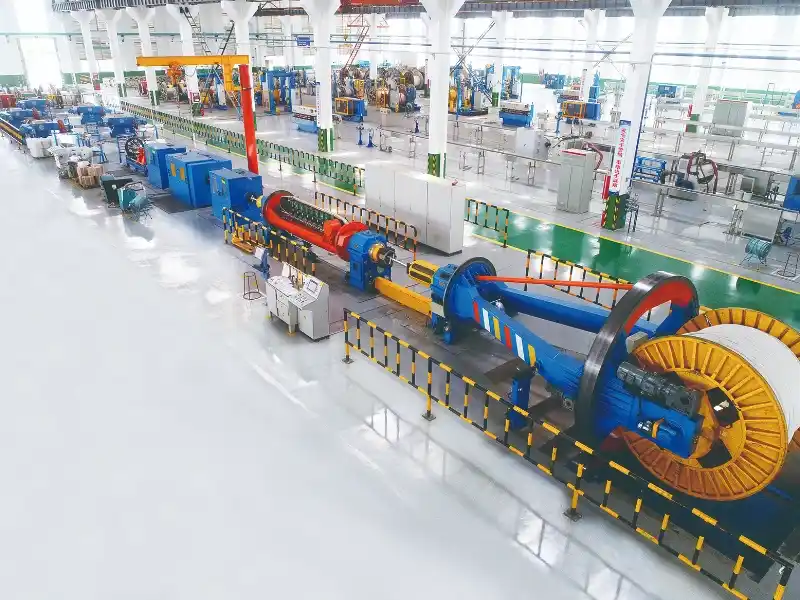
Single-Twist Drum Twisters
Description:
Single-twist drum twisters create a single twist in multiple wires around a common axis. This design is straightforward and is often employed for simpler twisting operations.
Mechanism:
Operation: The machine uses a rotating drum mounted on a fixed frame. As the drum rotates, it pulls the wires through a twisting mechanism that ensures even tension and consistent twist.
Components:
Rotating Drum: Central component that holds the wire and imparts the twist.
Feeding Mechanism: Guides the wire into the drum at a controlled speed.
Control Panel: Allows operators to adjust speed and monitor the process.
Advantages:
Simplicity & User-Friendliness: Easy to set up and operate, making it ideal for small-scale operations.
Cost-Effective: Lower maintenance and operational costs compared to more complex systems.
Ideal for Low-Volume Production: Suitable for specialized applications where high volume is not required.
Applications:
Copper and Aluminum Wires: Effective for creating twisted strands of these metals, commonly used in basic electrical wiring.
Multi-Stranded Cables: Essential for producing uniform multi-strand cables that require consistent twisting.
Double-Twist Drum Twisters
Description:
Double-twist drum twisters allow for twisting in two axes, resulting in a more complex and tighter configuration of the wires.
Mechanism:
Operation: The machine utilizes two rotating drums that work in coordination, allowing for a more intricate twist pattern.
Components:
Dual Drums: Provide the ability to create double-twisted pairs or multi-layer twists.
Advanced Control System: Offers programmable settings for different twisting patterns, speeds, and lengths.
Advantages:
Flexible Design: Capable of accommodating various wire types and sizes.
Enhanced Quality: Produces higher quality twisted pairs, reducing the risk of crosstalk in communication cables.
Versatile Applications: Can be configured for different production requirements.
Applications:
Telecommunication Cables: Crucial for producing twisted pairs that minimize electromagnetic interference.
Automotive Wiring: Used to create complex wiring harnesses that withstand vibrations and harsh conditions.
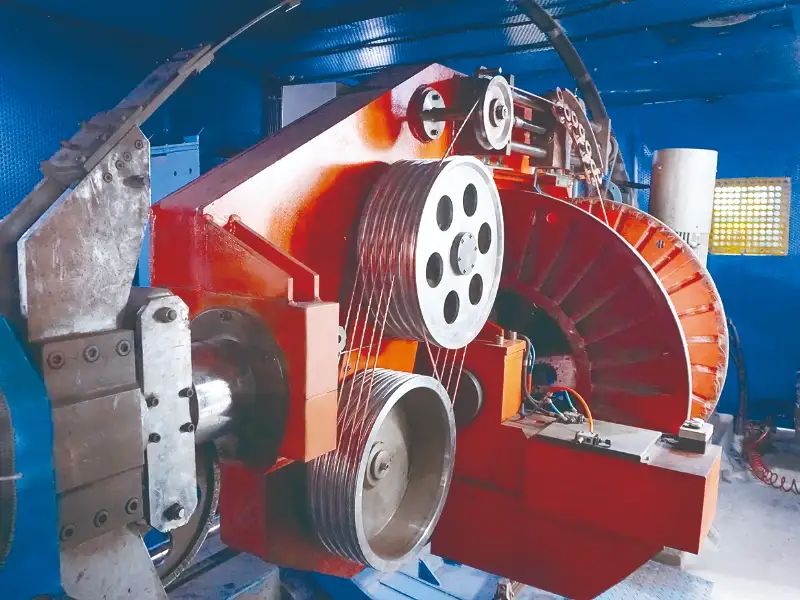
Electric Drum Twisters
Description:
Electric drum twisters employ electric motors, providing constant power and speed control for increased efficiency.
Mechanism:
Operation: The electric motor drives the rotation of the drum, allowing for precise control over twisting speed and tension.
Components:
Electric Motor: Provides power and consistency throughout the twisting process.
Digital Control Interface: Allows operators to set specific parameters for different wire types.
Advantages:
Automation: Reduces manual labor by automating the twisting process.
Consistent Output: Maintains uniform twist tension across long production runs.
Programmability: Users can save settings for different products, enhancing production efficiency.
Applications:
Mass Production: Widely used in large wire and cable manufacturing facilities, particularly for standard products.
Specialty Cables: Good for producing high-quality specialty cables that require precise specifications.
Pneumatic Drum Twisters
Description:
Pneumatic drum twisters operate using compressed air, making them suitable for environments where electric machines may pose safety risks.
Mechanism:
Operation: Compressed air powers the twisting mechanism, providing a clean and safe operation in hazardous environments.
Components:
Air Compressor: Supplies the necessary pressure for operation.
Pneumatic Actuators: Control the movement of the twisting mechanism effectively.
Advantages:
Safety: Ideal for use in environments with flammable materials or where electrical sparks are a concern.
High Torque: Delivers powerful twisting capabilities, suitable for heavy-duty applications.
Applications:
Industrial Cables: Commonly used for high-volume production of industrial-grade cables.
Heavy-Duty Applications: Effective in sectors like construction and mining that require robust wiring solutions.
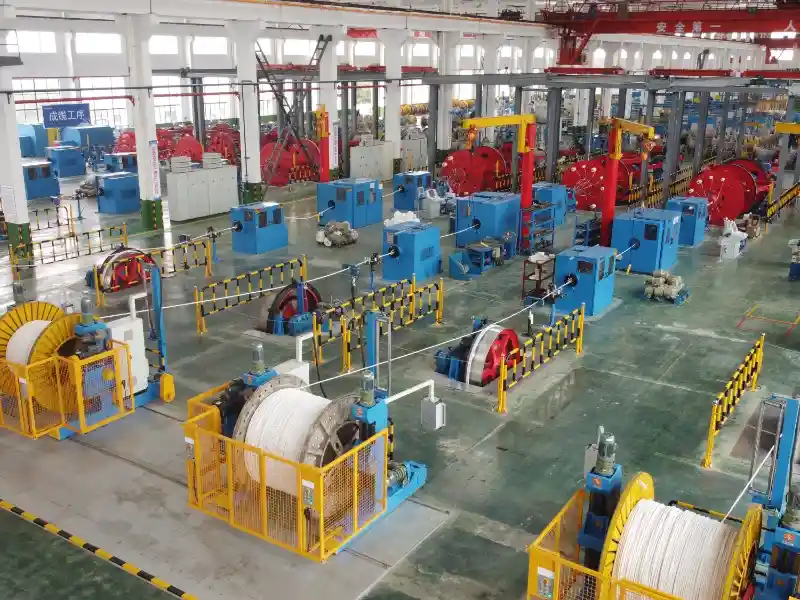
Hydraulic Drum Twisters
Description:
Hydraulic drum twisters utilize hydraulic systems for generating twisting force, making them suited for heavy applications.
Mechanism:
Operation: Hydraulics allow for high torque and smooth operation, especially when working with larger wire bundles.
Components:
Hydraulic Pump: Powers the twisting mechanism.
Hydraulic Cylinders: Facilitate the movement and twisting action.
Advantages:
Heavy Lifting Capacity: Designed to handle larger and heavier wire bundles without deformation.
Smooth Operation: Ensures consistent twisting without damaging the wire due to excessive tension.
Applications:
Large Gauge Wires: Perfect for industries requiring heavy gauge wires used in power transmission.
Robust Cable Assemblies: Used for creating durable cable assemblies needed for industrial applications.
Conclusion
The choice of drum twister—be it single-twist, double-twist, electric, pneumatic, or hydraulic—depends on the specific needs of the manufacturing process, including the type of wire, production volume, and desired characteristics of the final product. Understanding these differences allows manufacturers to optimize their operations and ensure high-quality output in the wire and cable industry. Investing in the right type of drum twister is crucial for maintaining efficiency, reducing costs, and meeting market demands.